How to Set up a QR Code System for Your Inventory
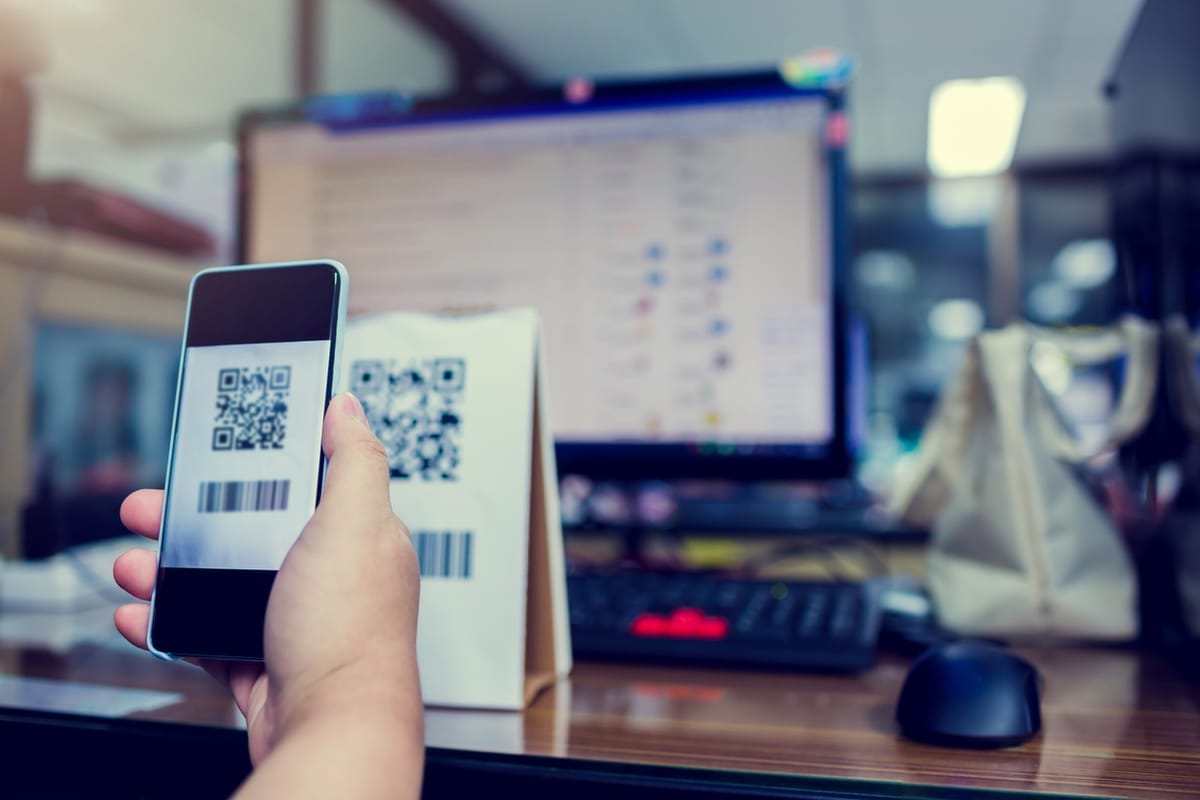
QR codes are everywhere, from marketing materials to product packaging and even restaurant menus. These compact, pixelated symbols have become a familiar part of our daily lives. But did you know they were originally created for inventory management? Invented in the automotive industry as a faster, more efficient alternative to barcodes, QR codes have since become a game-changer for tracking and organizing stock.
Incorporating QR codes into your business can help streamline your inventory process, reduce errors, and improve overall accuracy. In this article, we'll guide you on how to set up a QR code system to track and manage your inventory by using BoxHero's intuitive interface.
But first, let's take a quick look at what makes QR codes so effective for inventory management.
QR Codes: A Brief Introduction
A Quick Response (QR) code is a 2D barcode made up of a small, contrasting squares–often black and white–arranged in specific patterns. These squares store tons of useful information that you can instantly access by scanning the code, encoding data like URLs, text, images, and much more.
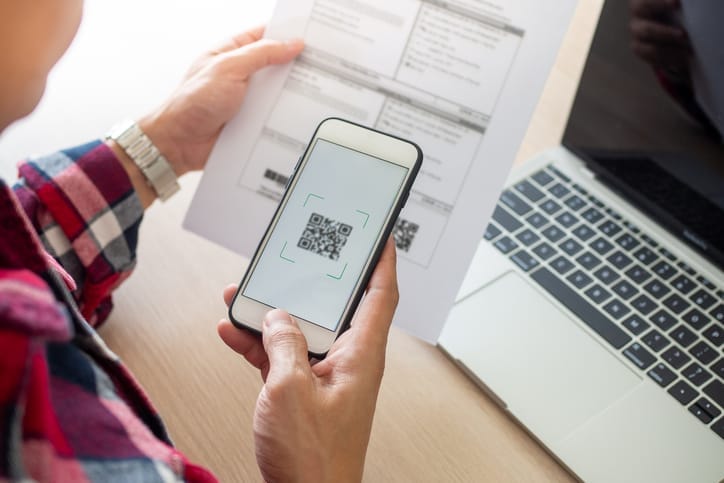
Read more: Barcodes vs. QR Codes: What's the Difference?
Static vs. Dynamic QR Codes: Which is Better?
Not all QR codes are created equal, especially when it comes to inventory management. There are two main types of QR codes: static and dynamic.
Static QR codes store fixed information that can't be edited once the code is created. They're useful for encoding data that doesn't change, like a product manual URL or a one-time event link. In addition, static QR codes can be accessed offline, which means you can use them in storage areas and other locations that may not have reliable WiFi.
The downside is that static QR codes can't be updated or tracked, making them less than ideal for inventory systems where data frequently changes.
This is where dynamic QR Codes come in. Unlike static codes, dynamic QR codes allow you to update the encoded information even after the QR code has been printed. This makes it easy to track and manage changing details–such as stock levels, prices, or warehouse locations–without needing to create a new QR code.
By storing both fixed information (like product names or SKUs) and dynamic data (like stock quantities or pricing), dynamic QR codes offer a flexible solution for inventory management.
Why Should You Use a QR Code System to Manage Inventory?
Now that you know what QR codes are, let’s explore why they make an excellent choice for managing your inventory.
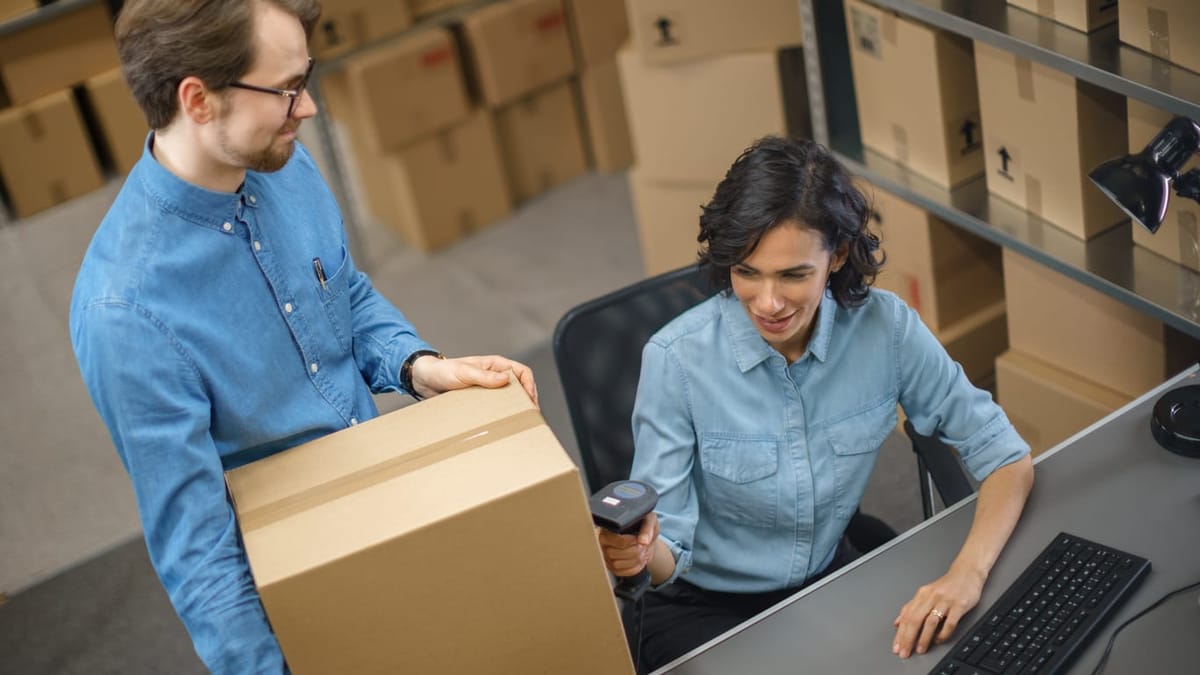
▶︎ Stores a Wealth of Information
One of the biggest advantages of QR codes is that they can store a vast amount of product information in a compact space. With just a single QR code, you can access key details like:
- SKU
- Product/item name
- Product/item description
- Quantity
- Supplier or vendor information
- Cost & price
- Location
What would typically require multiple barcodes to convey can now be packed into a QR code, saving valuable space on your shelves and simplifying your inventory labeling system.
▶︎ Reduces Paperwork
Another benefit of QR codes is that they can help you replace the clutter of bulky record books and filing cabinets with digital records of your inventory data. When paired with a reliable inventory management software like BoxHero, QR codes can help you track stock movements and generate real-time reports.
Not only do QR codes save valuable physical space, but they also provide greater security in the long run by storing information digitally. Unlike paper records that are prone to damage from wear and tear, digital data is much easier to protect and maintain over time.
Moreover, relying on manual data entry for inventory can lead to costly errors. By using QR codes, you can reduce the risk of human error and streamline your inventory management, ultimately saving your business both time and money.
▶︎ Prints Flexible Labels
In addition to reducing errors, QR codes are flexible for inventory labeling. Whether you're working with limited label space or need a larger printout for easier scanning, you can adjust the size of QR codes to fit your needs.
Print Barcode
feature, you can choose choose between Raster or Vector. While both options work well, it's best to choose the Vector format for printing physical labels so that your QR code stays sharp and scannable, even when resized. 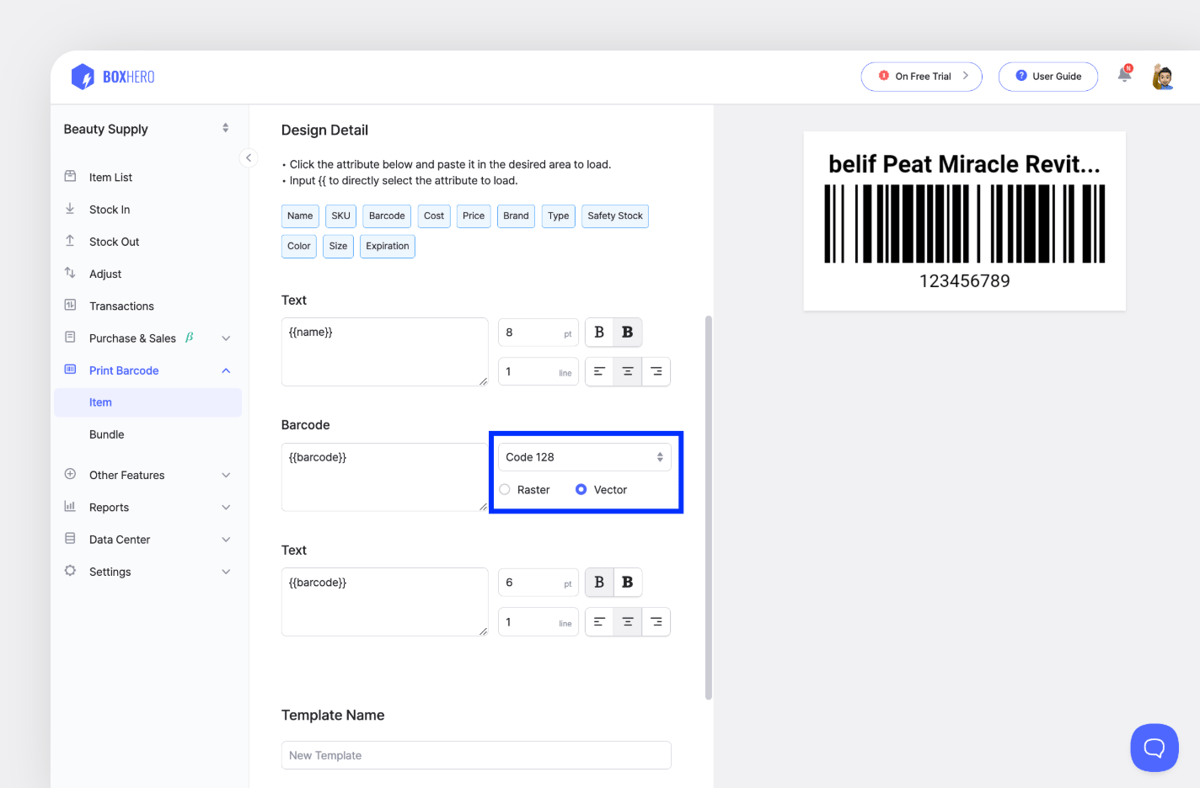
▶︎ Simplifies Inventory Location Tracking
Beyond labeling flexibility, QR codes also make it easier to manage multiple storage locations for your inventory. With QR codes, you can update an item's location details and track stock movements in real-time. This helps prevent phantom inventory, which can lead to lost sales and frustrated customers.
Maintaining accurate location tracking is easy with BoxHero’s Location Mode, where you can add new locations for your shelves, stores, and other physical spaces. With QR codes, you'll have a clear, up-to-date view of your stock across all your sites.
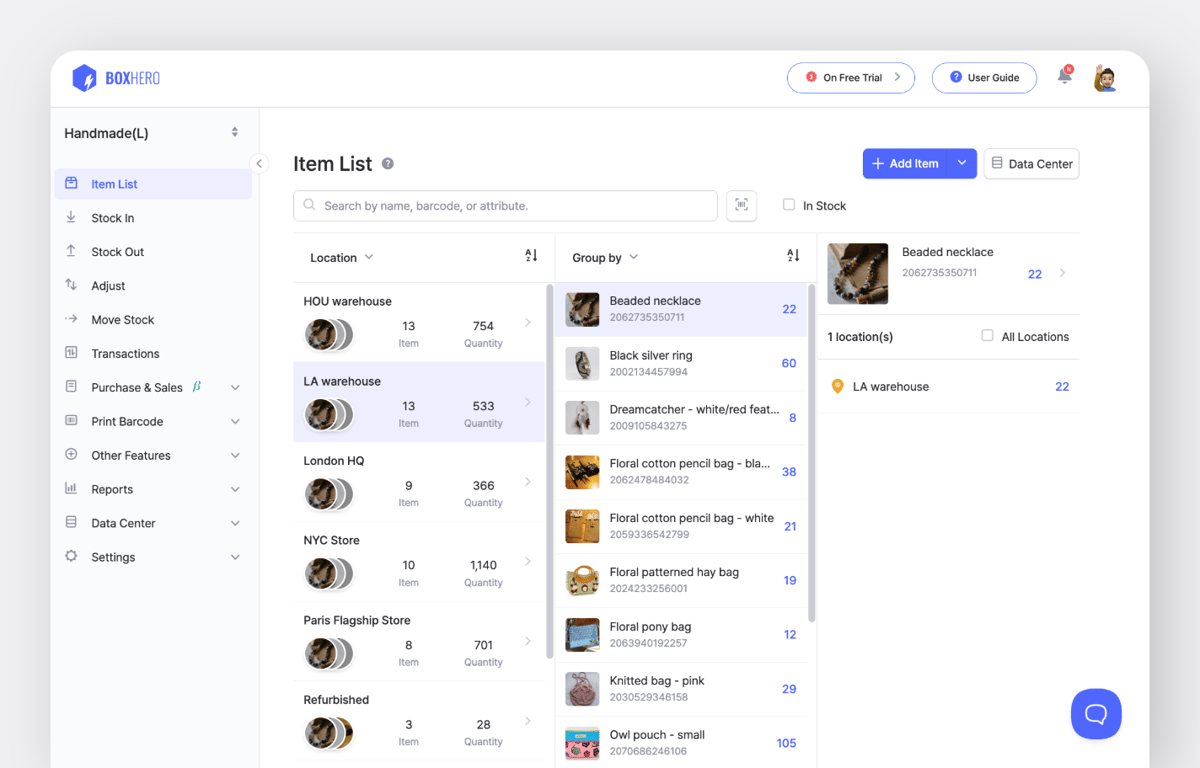
Read more: Three Practical Ways to Make Use of Location Mode
How to Set Up a QR Code System for Your Inventory (with BoxHero!)
Step 1: Plan Your Inventory System Requirements
Before we start creating QR codes for your inventory, it's best to outline the key aspects of your new QR code-based inventory system first.
To get started, you'll need to decide on the following:
- The item information you want to track using the QR codes
- Your inventory management software (BoxHero, in this case!)
- The locations where you'll track your inventory
Step 2: Generate QR Codes for Your Items
Barcodes and QR codes are key to an efficient inventory management system, and the good news is, you can easily generate them directly in BoxHero.
When registering a new item on your Item List
, enter your existing barcode number under Item Information. You can manually type it in, or use a barcode scanner or even your smartphone camera to scan and pull up the barcode details. BoxHero supports multiple devices, so you can do this both on the PC version and the mobile app for convenience.
BoxHero can create one for you! Click the green "Generate" button next to the Barcode field and BoxHero will automatically create a unique 13-digit barcode number, which will then be used to generate the corresponding QR code when you're ready to print your labels.
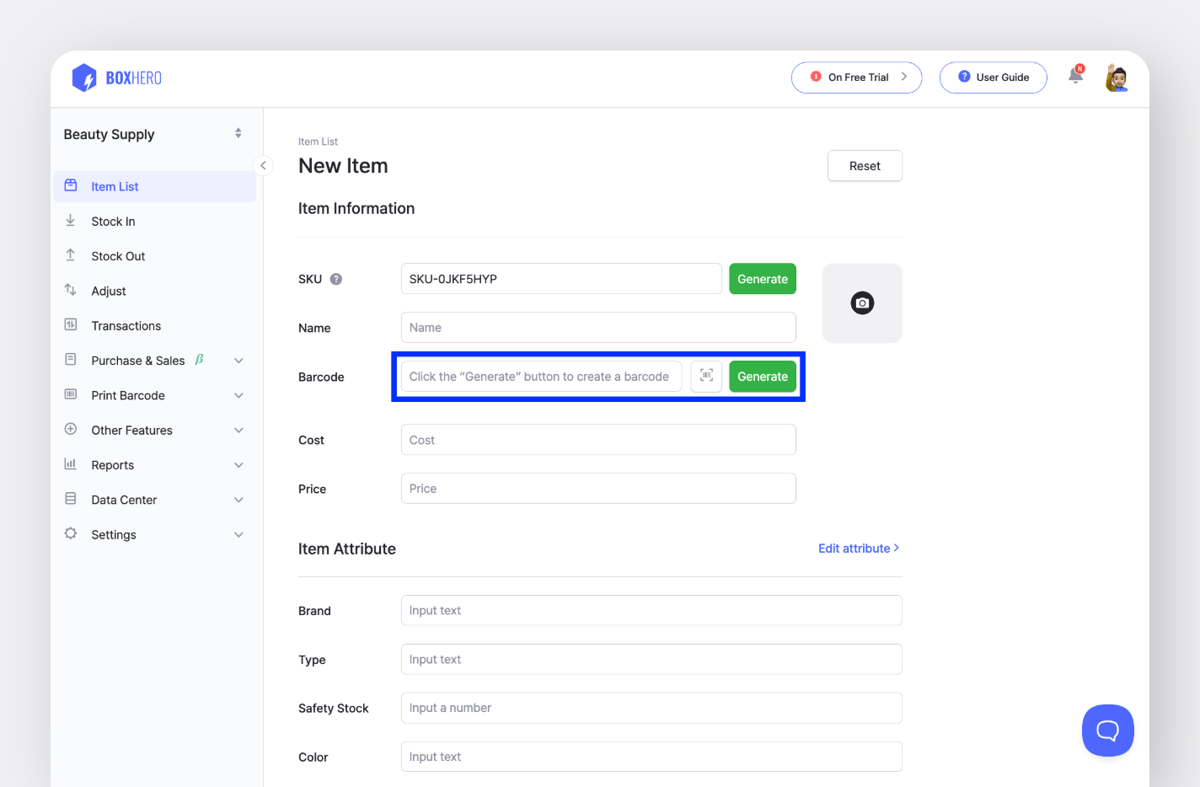
Step 3: Print Your QR Code Labels
Now that you’ve got a QR code for each product, it’s time to print those codes onto labels for easy scanning and organization.
Key details to decide before printing:
- Printing Paper: Choose the appropriate printing paper, such as thermal paper or label sheets. Make sure the paper is compatible with your printer and durable enough for your environment.
- Label Size and Design: Decide on the size and design of your labels. Consider the space available on your products or shelves, and choose a design that includes clear, legible QR codes.
- Number of Labels per Product: Determine how many labels you need per item, based on the number of locations or containers you’ll be labeling.
BoxHero has a built-in barcode printing feature that prints not just 1D barcodes but also 2D barcodes (i.e. QR codes) and text-based labels for your products. If you’re already using BoxHero for inventory management, you can easily print your QR code labels directly from the platform.
Don't forget to check out BoxHero's free barcode generator, which lets you create barcodes by uploading your items via Excel!
Read more: BoxHero’s Improved Barcode Printing Feature
Step 4: Attach the QR Code Labels
Once you’ve printed your QR code labels, it’s time to attach them to your products. The great thing about QR codes is that they can be scanned from any angle, so you have flexibility in where to place the labels. Just avoid sticking them on seams or areas that might crease or get damaged so you don't end up with worn-out labels that need to be reprinted.
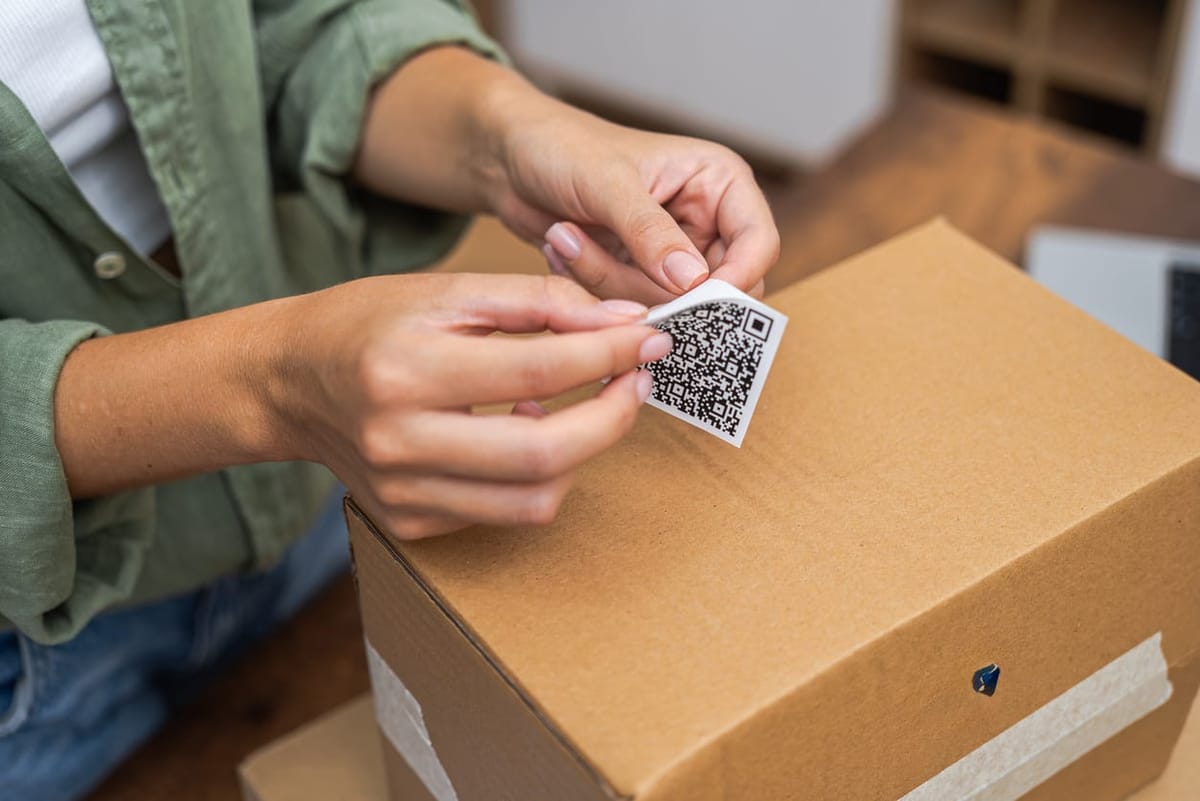
Step 5: Set Your Team Up With the New Inventory Management System
With your labels securely attached, it’s time to get your team up to speed. Make sure everyone understands how to use the new QR code system for managing inventory. Proper training on how to scan items, update stock levels, and track stock movements in BoxHero will help you and your team make the most out of your new inventory system.
Invite your staff to join your BoxHero account and grant custom permissions based on their specific roles and responsibilities! If you have company tablets or smartphones, we recommend installing the BoxHero app so you can demonstrate how the new QR code system works.
If you're ready to simplify and automate your inventory management system with QR codes, BoxHero is the all-in-one solution you've been looking for.
Sign up today for a free trial and explore BoxHero's powerful features to take your first step towards more efficient inventory management!