Bill of Materials (BOM) Explained: What It Is and Why It’s Important
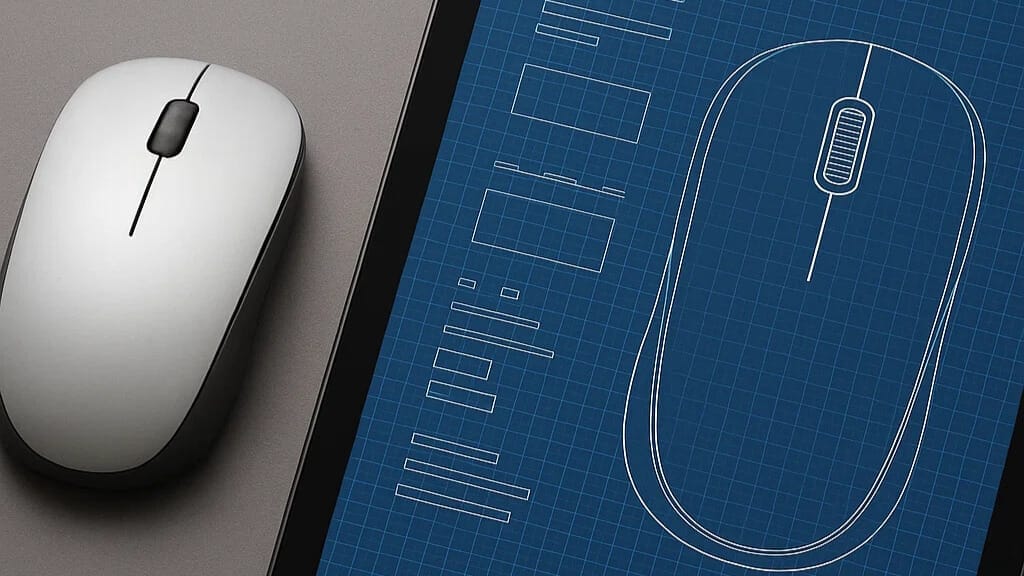
If you're involved in manufacturing or selling physical products, you've probably come across the term "Bill of Materials," or BOM. Think of it as your product’s recipe—a detailed inventory of everything needed (steps included!) to create your final product. Without a clear BOM, even small mistakes in production can quickly escalate and lead to big issues like inventory mismatches or production delays.
In this article, we'll dissect what exactly a BOM is, how different industries use BOMs, and share practical tips to help your team manage them more efficiently.
What is a Bill of Materials (BOM)?
A Bill of Materials is simply a detailed list of parts, components, and materials required to build your product.
Remember the recipe analogy? Imagine trying to bake a cake without a clear recipe. You might be able to guess the ingredients, but you'll need clear instructions and measurements to successfully bake the cake. Similarly, without a clear BOM, your team may struggle with inventory discrepancies, assembly errors, and ultimately, compromised product quality.
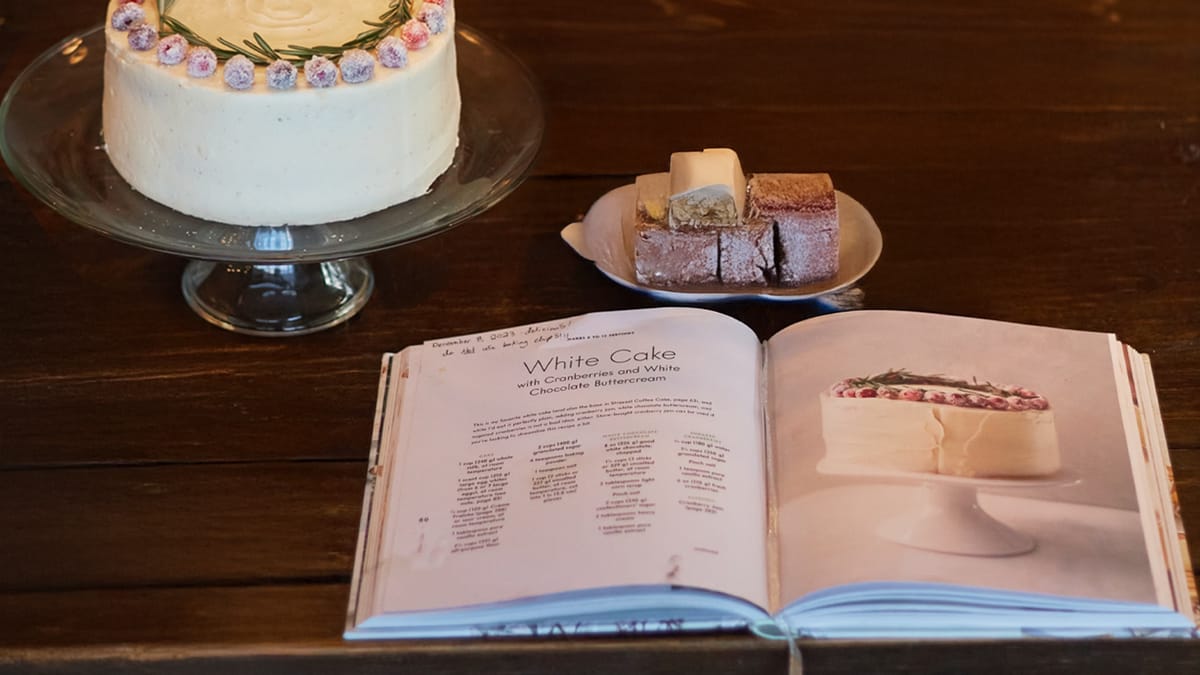
A BOM typically includes:
- Item numbers
- Clear descriptions of each part
- Quantities needed
- Unit of measure (UoM)
- Specific part numbers or identifiers
- Assembly instructions or special notes
Types of BOMs & When to Use Them
Choosing the right type of BOM depends on your product complexity: What are your businesses' specific needs? At which stage of the product lifecycle are we looking at?
1. Single-Level BOM
A single-level BOM lists all components needed for a product without breaking them down into smaller components. It works best for simple products with straightforward assembly, like a wooden chair from IKEA with a required defined set of parts and no sub-assemblies.
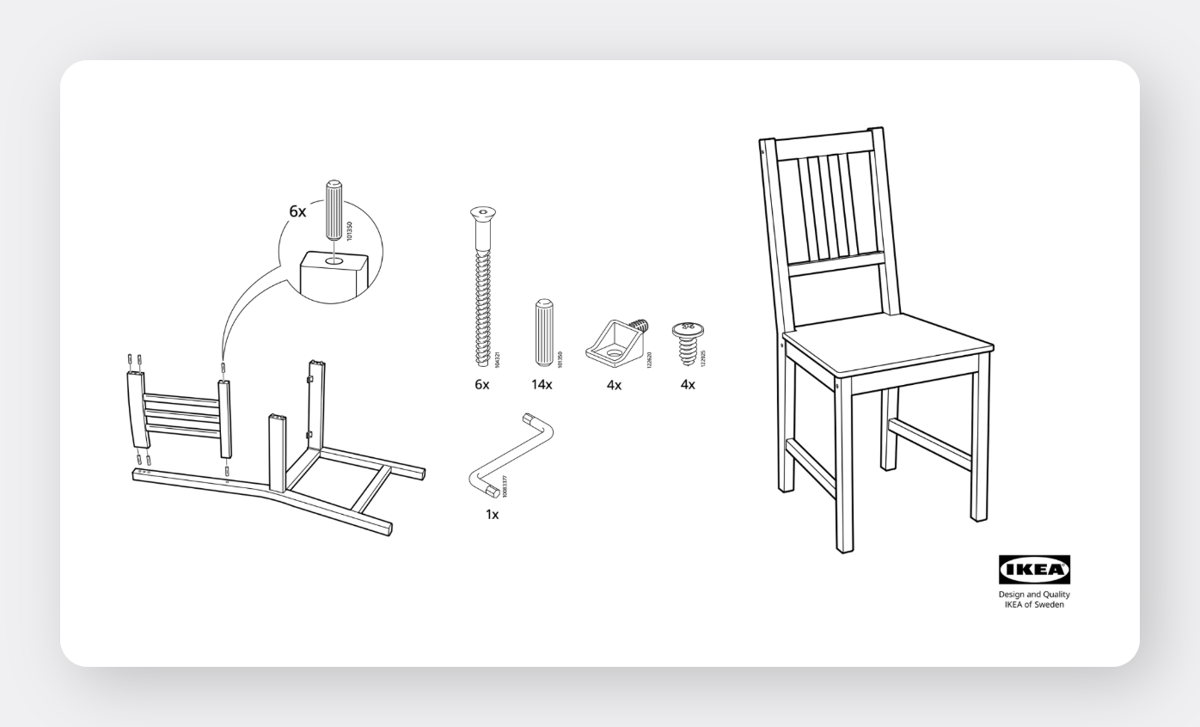
Best for: Products like a basic chair (legs, seat, back, screws) or a simple promotional kit.
2. Multi-Level BOM
Multi-level BOMs provide detailed breakdowns of all sub-components and sub-assemblies, clearly illustrating how parts fit together. They're ideal for complex products with multiple stages or assemblies, such as electronic devices or vehicles, where multiple assembly stages occur.
For example, cars have multi-level BOMs outlining parts required for the engine (which itself is a sub-assembly with its own BOM), transmission, chassis, and interior systems.
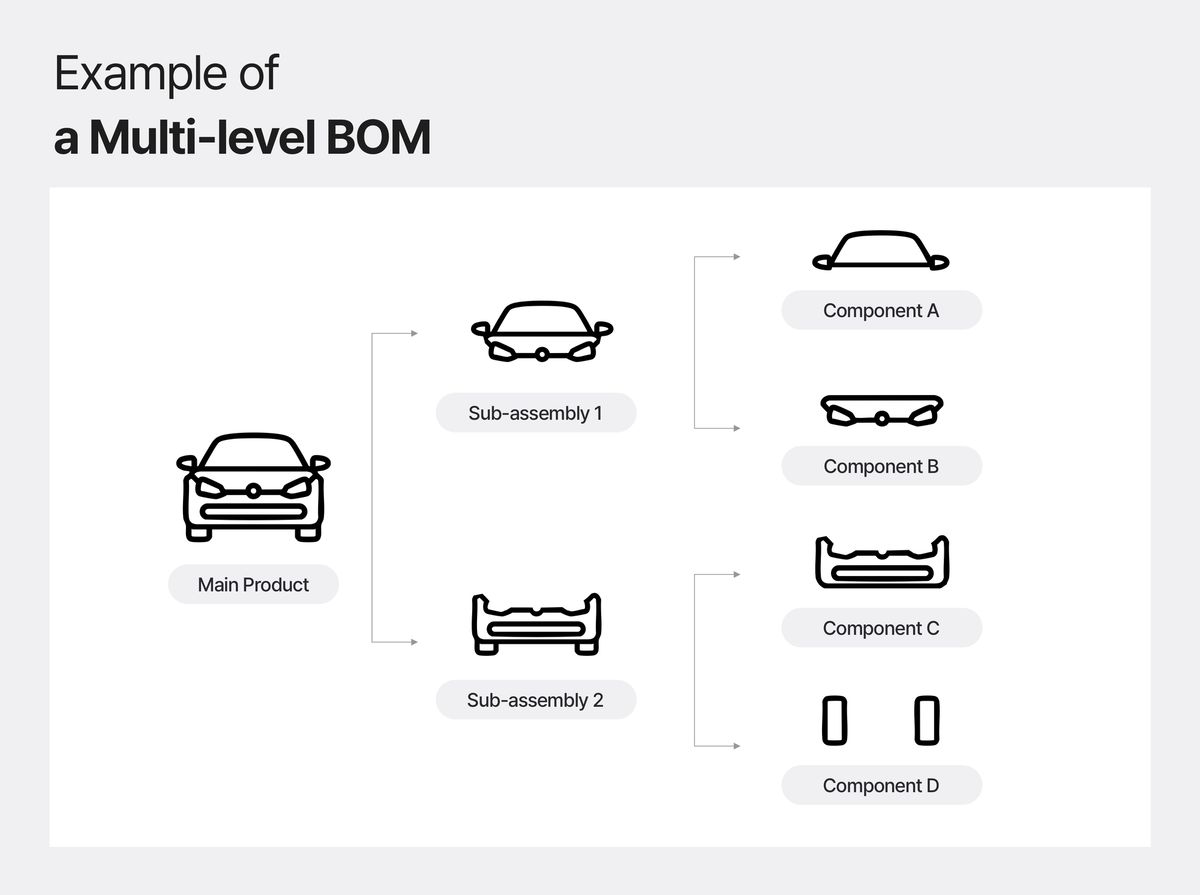
Best for: Complex machinery, electronic devices, or vehicles where multiple assembly stages and sub-components are involved.
3. Engineering Bill of Materials (EBOM)
EBOMs focus on product development and are usually created directly from design tools like Computer-Aided Design (CAD) software. They reflect the product as designed by engineers, focusing on technical specifications, component relationships, and design integrity.
Best for: Product development, prototyping, and ensuring design specifications are met.
Companies like Tesla and Boeing rely heavily on EBOMs generated from software like SolidWorks and AutoCAD. These EBOMs ensure every technical detail and component fit is correctly captured before physical prototyping or manufacturing begins.
4. Manufacturing Bill of Materials (MBOM)
MBOMs reflect the actual manufacturing process. They list all parts and assembles required to build a shippable product and arrange these components in the exact order they're used on the shop floor. MBOMs can differ from EBOMs because production may require parts in a different order, grouping, or sequence.
For instance, an MBOM for a smartphone manufacturer like Samsung would clearly outline the sequence in which internal components like batteries, processors, and screens are assembled.
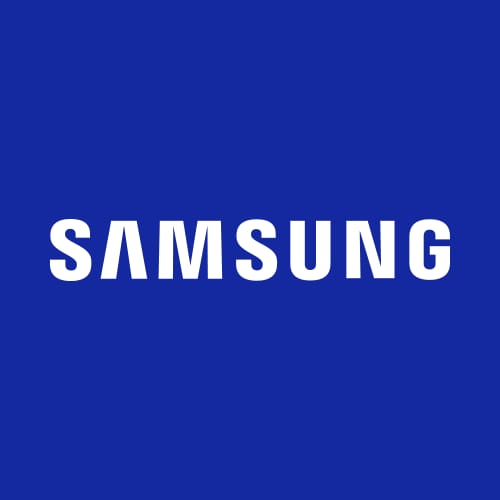
5. Sales Bill of Materials (SBOM)
SBOMs define products as they are sold. They're particularly useful for items sold as kits or bundles, where the final "product" for the customer consists of multiple individual items.
Take promotional product sets, gift boxes, or accessory bundles, for example. Many cosmetic brands frequently use SBOMs to sell product bundles such as makeup kits, gift sets, and starter packs.
Best for: Sales order processing, product catalog management, and marketing bundled offerings.
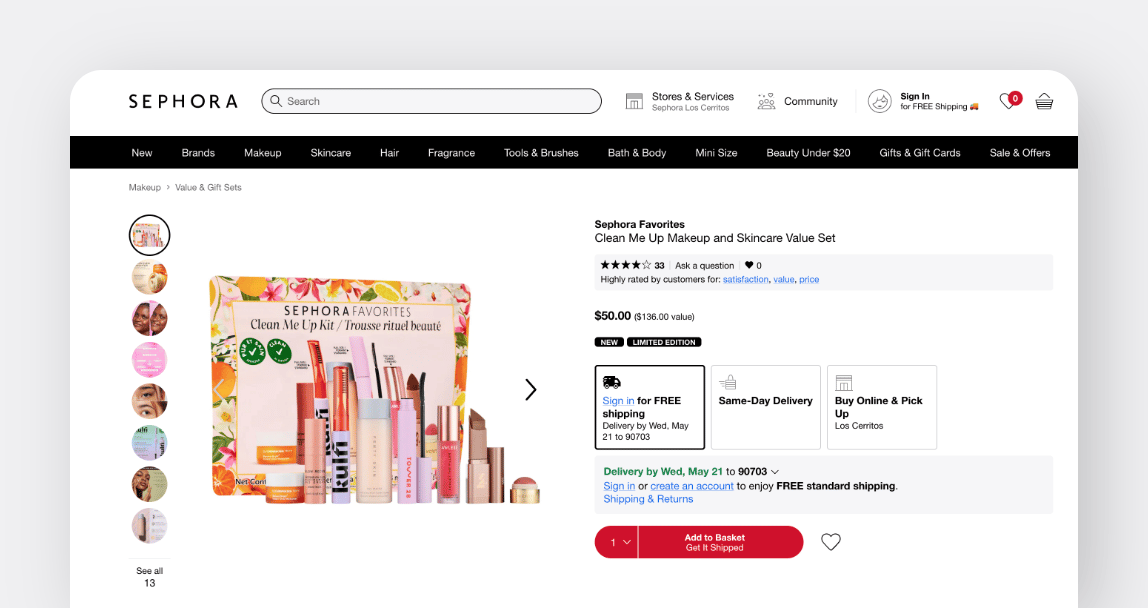
Learn more about managing bundled products:
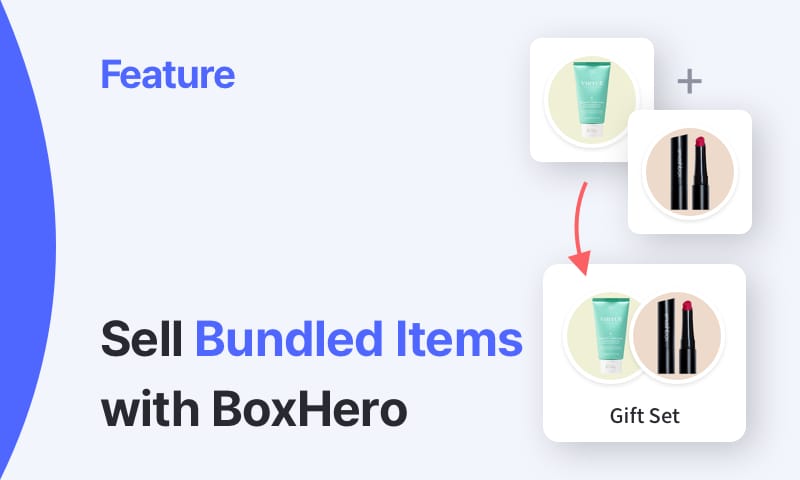
Why is a BOM Important?
A well-managed BOM is a strategic asset that positively impacts multiple facets of your business:
▶︎ Inventory Management
Accurate BOMs are fundamental to optimizing inventory. As highlighted by supply chain solutions provider Netstock:
"BOMs outline precisely what materials are needed to prevent overstocking or shortages. This keeps stock accurate, reducing holding costs and stockouts."
They cite a case study where proper BOM integration led to a 25% reduction in excess inventory and a significant improvement in fill rates. This means good BOM management reduces excess stock (and the capital tied up in it) and prevents stockouts that halt production or disappoint customers.
More efficient use of storage space and less waste—it's a win-win!
▶︎ Cost Tracking
Businesses tracking detailed BOM data also get a clear picture of their actual production costs. As TSTRONIC, an electronic manufacturing services provider, explains:
"A detailed BOM cost analysis provides a window into the total cost makeup of a product, breaking it down into cost categories such as direct material, indirect material, labor cost, and overhead."
If you're a small business owner, an accurate BOM will help you identify potential cost savings, improve profit margins, and make smarter financial decisions.
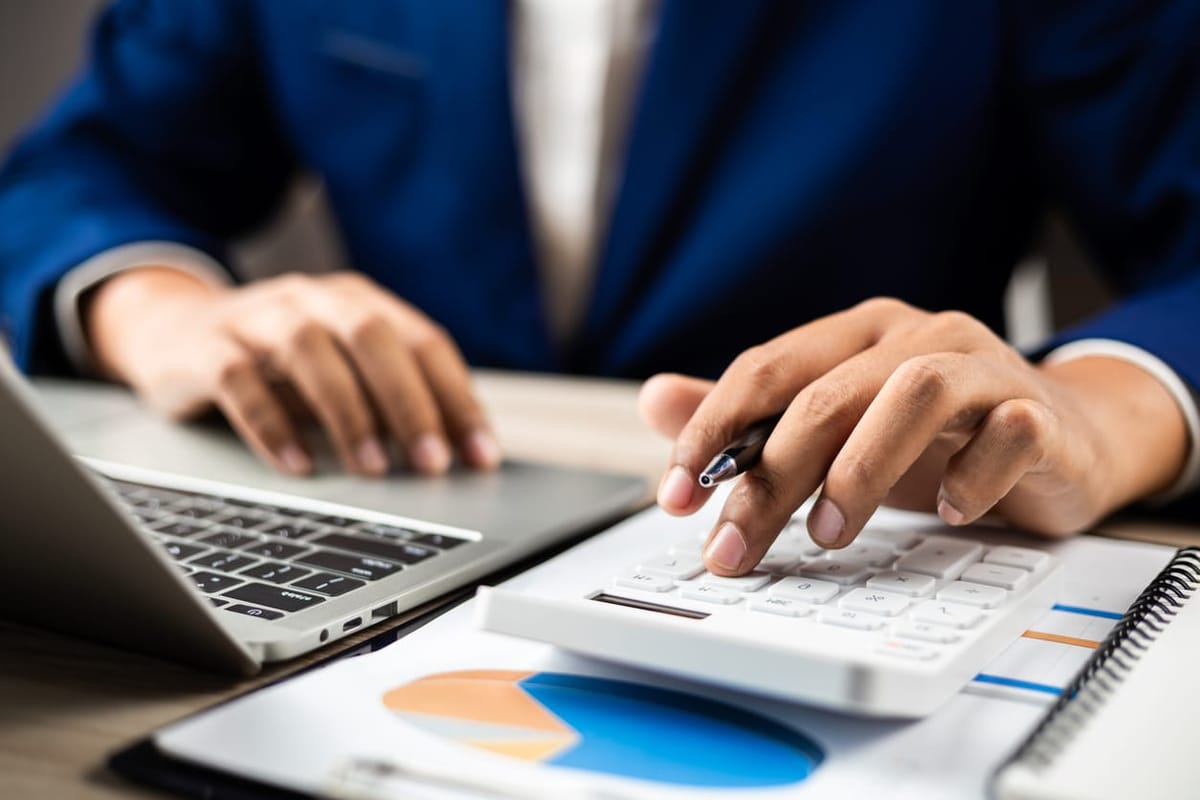
▶︎ Production Planning
Clearly structured BOMs also simplify production scheduling and make sure materials arrive on time (Just-in-Time principles).
As stated by PandaDoc:
"A BOM is the blueprint for production planning, detailing every part, raw material, and step in the manufacturing process," which helps "create timelines and processes to ensure teams stay on schedule."
Accurate BOMs prevent material shortages and ensure all necessary components are available, which directly minimizes production downtime and enhances overall productivity.
As anyone who’s managed a production floor knows:
= higher output,
= better resource utilization,
= and improved customer satisfaction.
▶︎ Regulatory Compliance
Let's not forget about compliance—Industries with strict regulatory requirements, like automotive, aerospace, and pharmaceuticals, depend heavily on accurate BOMs to maintain compliance and avoid costly recalls or legal penalties.
For instance, accurate BOM documentation helps pharmaceutical companies ensure that products meet FDA standards by clearly tracking all ingredients and manufacturing processes. This traceability is essential for quality assurance and patient safety so that you and I can trust that each pill we take contains exactly what it should (!)
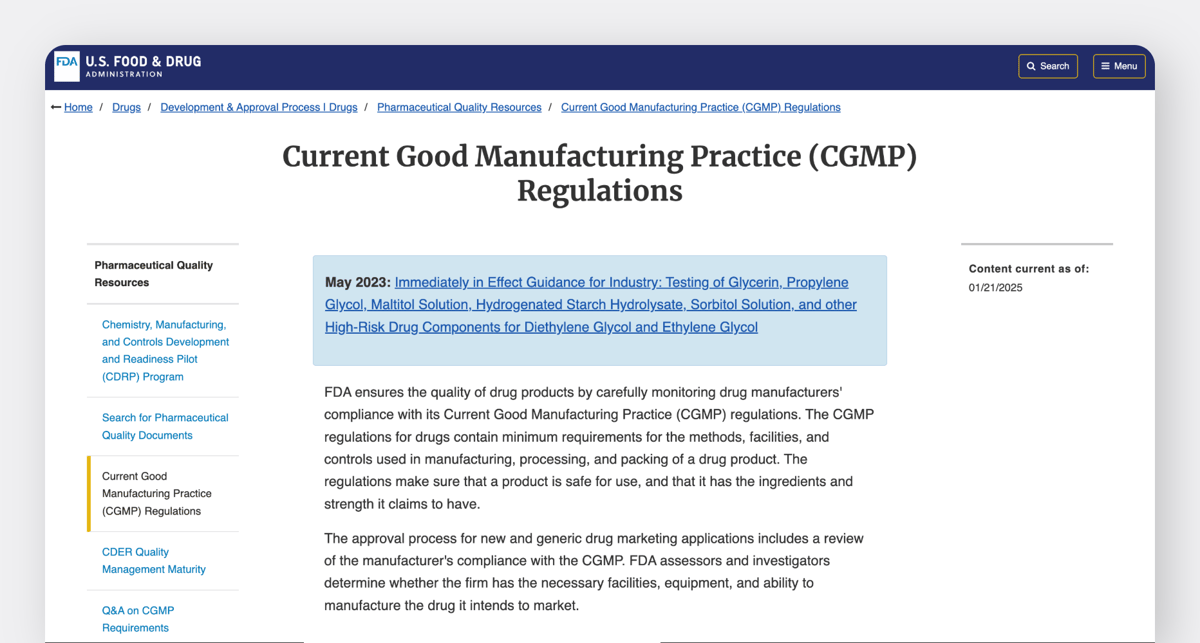
In these regulated fields, BOM accuracy is non-negotiable. A seemingly minor error, like listing the wrong grade of a material or an incorrect procedural note, can cascade into regulatory violations, multi-million dollar recalls, and severe safety risks for consumers.
How are BOMs Used Across Industries?
To truly grasp the strategic value of a BOM, let's look at how it functions across different industries.
Automotive Manufacturing
Automotive companies like Toyota famously integrate detailed multi-level BOMs into their Just-in-Time (JIT) production model. This allows them to keep minimal inventory and maintain efficient production lines to respond flexibly to market demands.
For years, Toyota has achieved significant waste reduction, minimized storage costs, and improved production velocity through BOM accuracy.
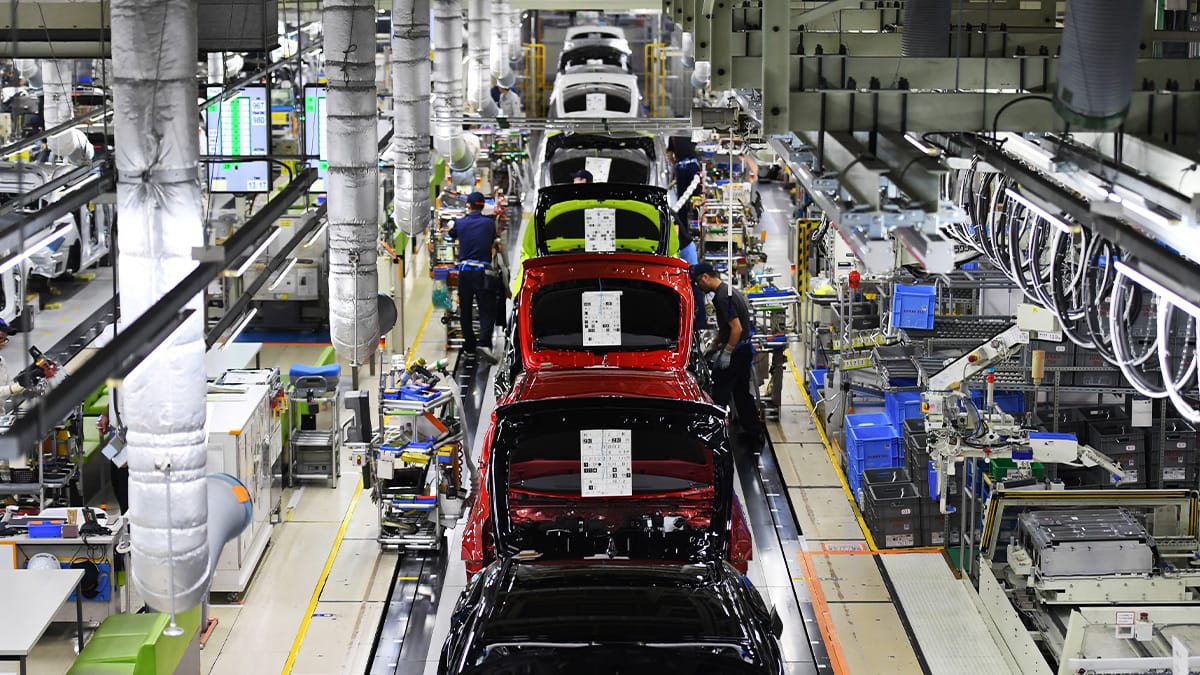
Electronics Industry
Tech giants such as Apple and Google manage incredibly complex global supply chains and rapid product innovation cycles. Accurate, dynamic BOMs help them coordinate thousands of components from diverse suppliers, manage frequent design updates (engineering changes), and ensure consistent product quality across vast manufacturing volumes.
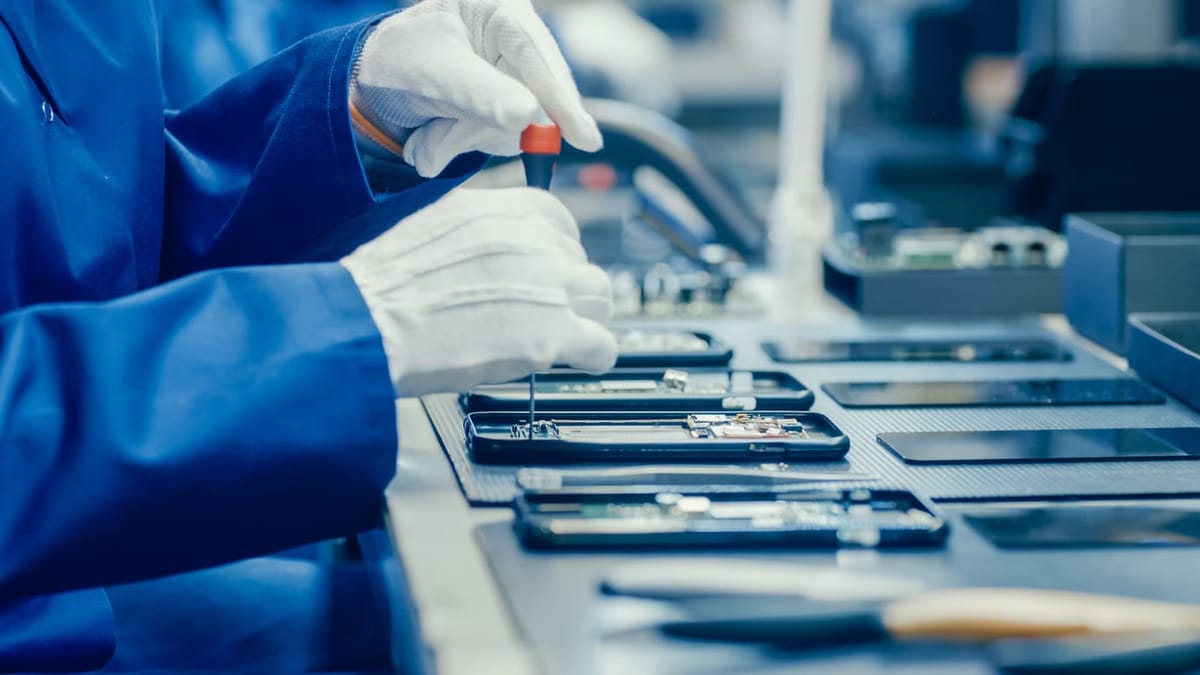
An error in the BOM for a device with millions of units in production could have huge financial and reputational consequences.
Food & Beverage
Food manufacturers rely on BOMs (often called "recipes" or "formulas" in this context) for product consistency, quality control, and regulatory adherence. BOMs clearly document ingredients, quantities, packaging materials, and nutritional information.
For example, a large bakery chain uses precise BOMs to ensure every loaf of bread meets taste, texture, and allergen labeling requirements consistently across all its production facilities. This also aids in accurate costing per unit and managing ingredient shelf-life.
Related: Comprehensive Guide to Managing Restaurant Inventory
Effective Ways to Manage Your BOM
Managing BOMs effectively requires a combination of robust processes and the right tools. Moving from reactive fixes to proactive BOM management can prevent delays and errors while giving teams better control over production and sourcing. Here's how:
1. Centralize Your Info
Use a central system, whether it's a dedicated BOM software, ERP module, or capable inventory management system like BoxHero. This creates a single data hub that simplifies access, maintains data consistency, and reduces errors from disparate spreadsheets or outdated documents.
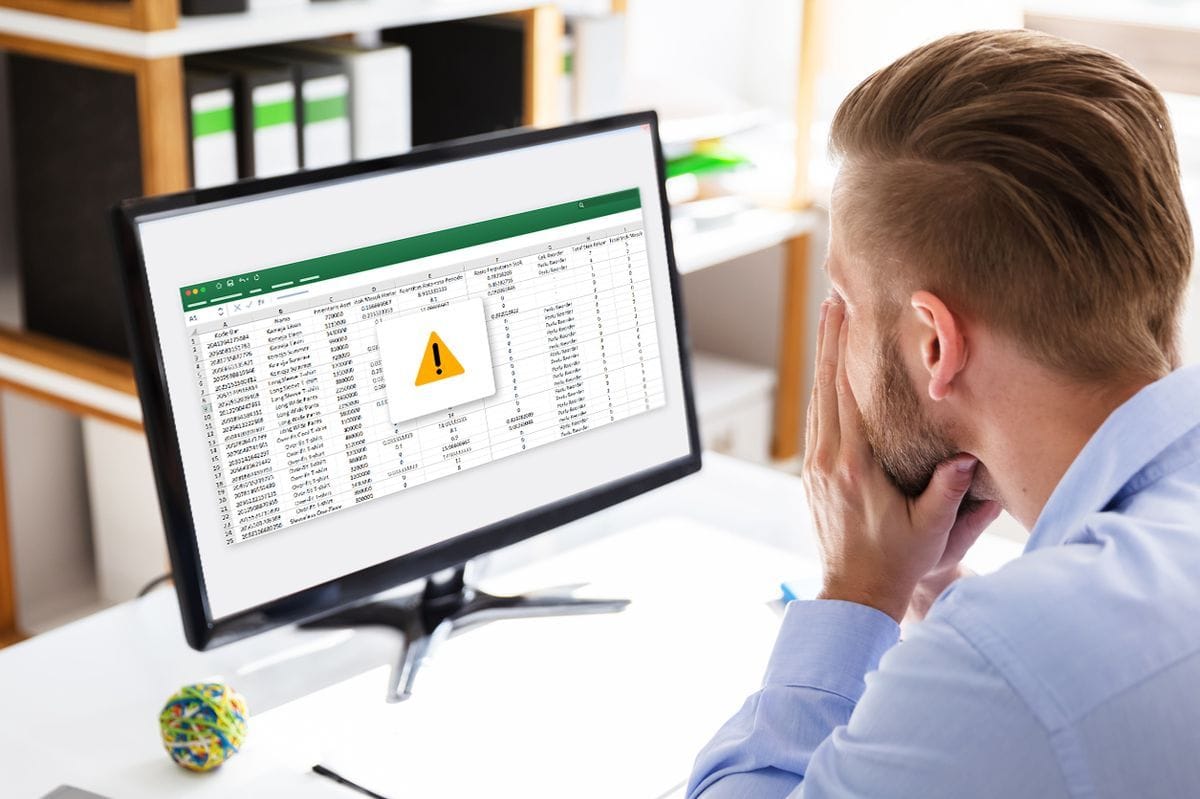
2. Update Regularly
Establish a formal process for BOM updates. Promptly update any changes in suppliers, materials, designs (Engineering Change Orders - ECOs), or manufacturing methods. You'll avoid production errors, obsolete inventory, and procurement of incorrect parts.
3. Use Cloud-Based Tools
Cloud solutions allow real-time collaboration across departments (engineering, procurement, production, sales) and even with external partners. As Tech-Clarity’s 2023 report highlights, businesses using cloud-based solutions for product development and manufacturing data management see significant improvements in efficiency due to better accessibility and version control.
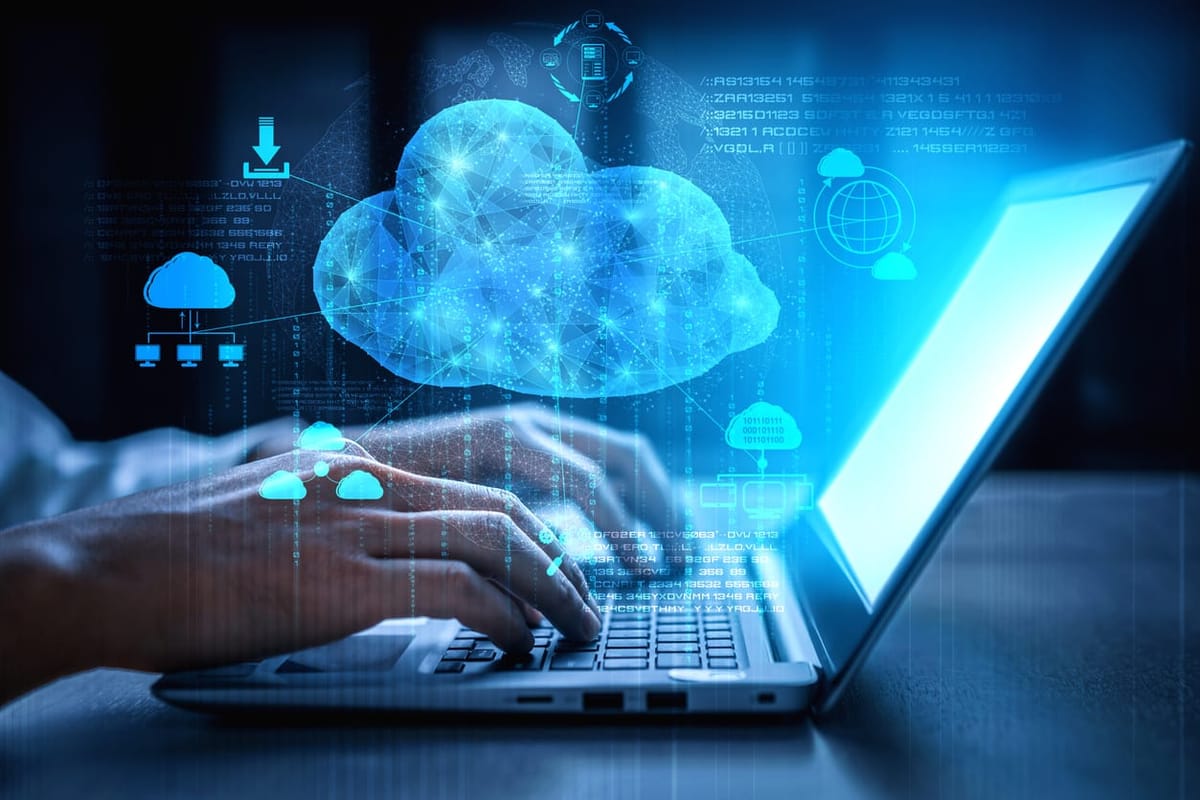
4. Use Clear Descriptions
Make sure to use clear, unambiguous, and detailed descriptions for all parts and materials in your BOM. Standardized naming conventions and attributes prevent misunderstandings during procurement, receiving, and assembly.
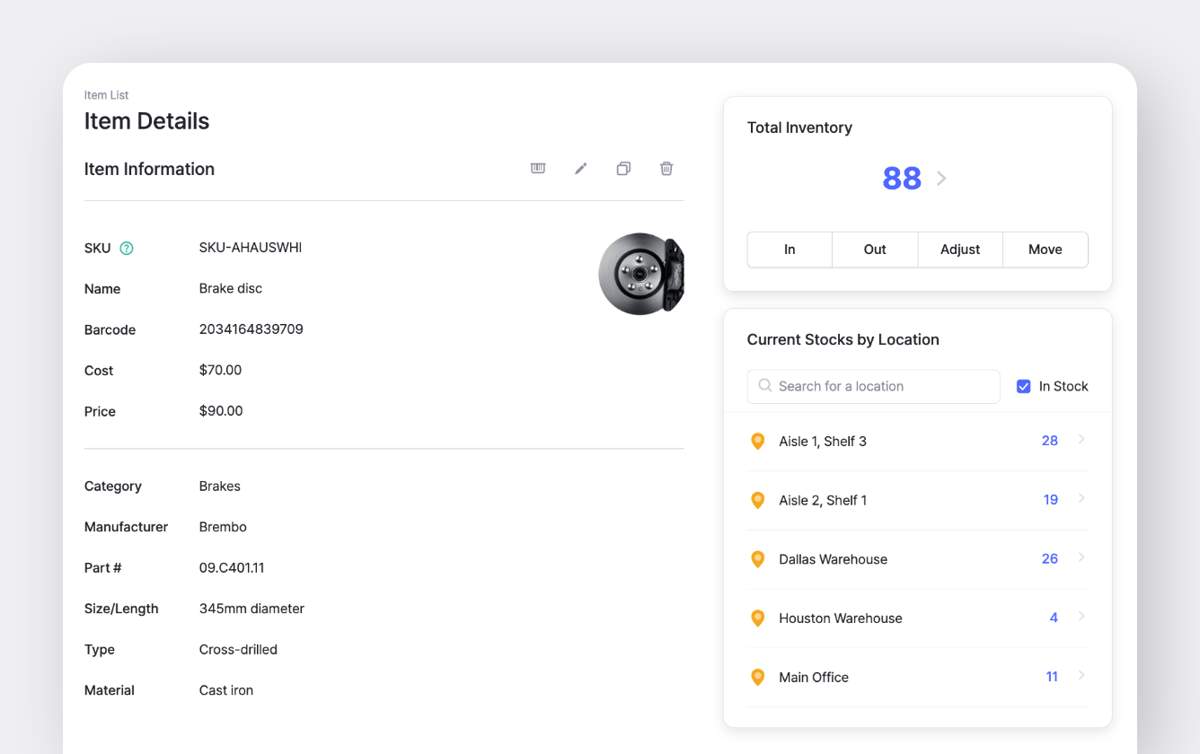
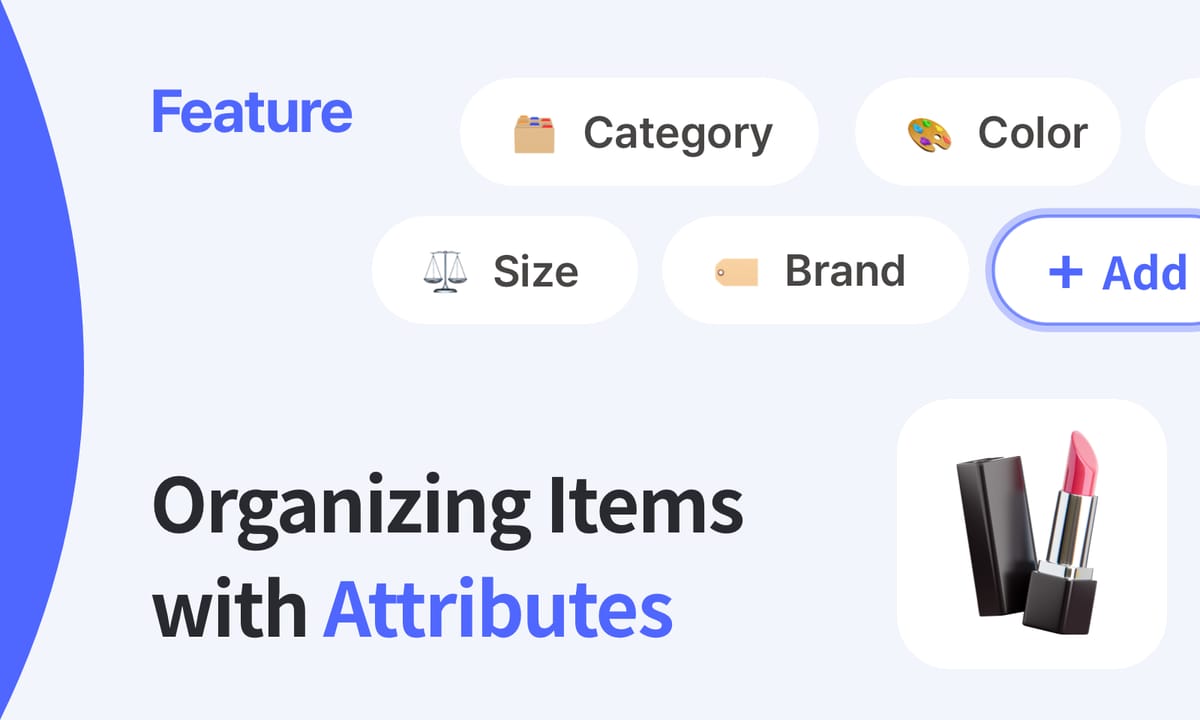
5. Include Alternative Parts
Where feasible, identify and approve alternative or substitute components. Including these in your BOM (perhaps with preference rankings) provides flexibility and helps prevent production delays when primary parts are unavailable. Even during supply chain disruptions, you'll be able to maintain consistent production flow!
Technology's Role in Managing BOMs
To support this shift toward a more proactive approach, many businesses are turning to technology. Modern software tools like Enterprise Resource Planning (ERP), Product Lifecycle Management (PLM), and specialized inventory management platforms have transformed the way we manage BOM.
These systems typically provide:
- Real-time inventory tracking linked to BOM consumption.
- Automated purchasing based on BOM requirements and stock levels.
- Effective departmental collaboration through shared data.
- Version control and engineering change management.
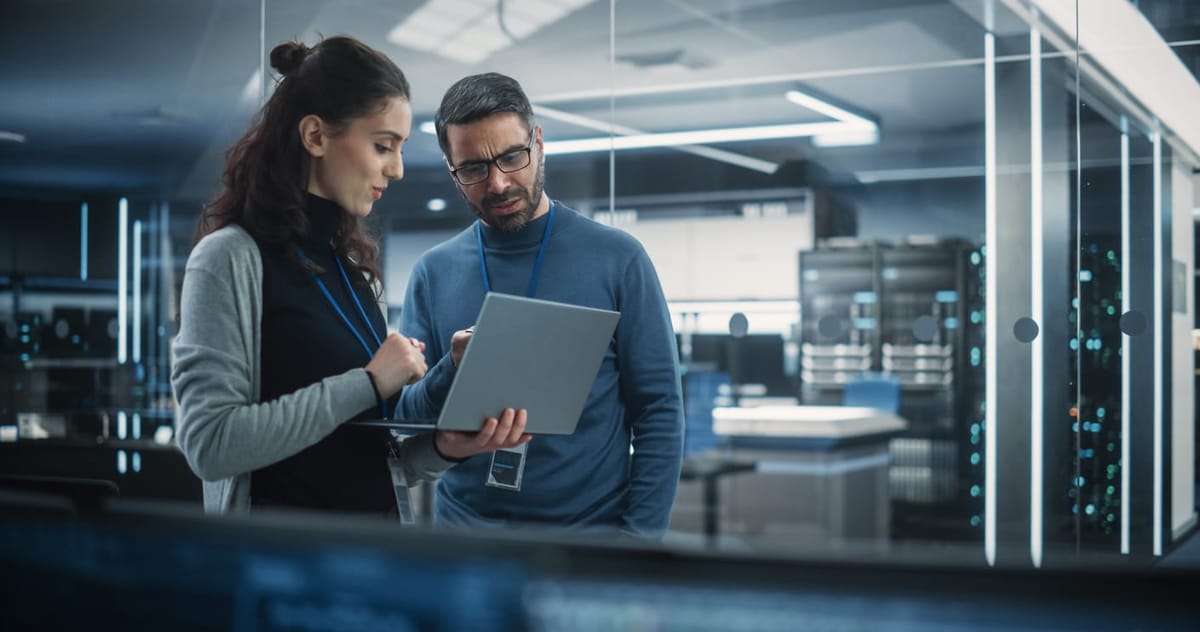
Effective BOM management within such systems ensures that all stakeholders are working from current data, streamlining handoffs between design, engineering, and manufacturing.
Common BOM Challenges & Solutions
Despite their importance, managing BOMs can be challenging:
- Handling Complexity: Multi-level BOMs for intricate products can become unwieldy without proper tools and structure.
- Keeping BOMs Updated: Rapid design changes, component obsolescence, or supplier shifts can make constant updates challenging.
- Ensuring Integration: BOM data often needs to flow between different systems (CAD, PLM, ERP, MES). Lack of integration leads to data silos and inaccuracies.
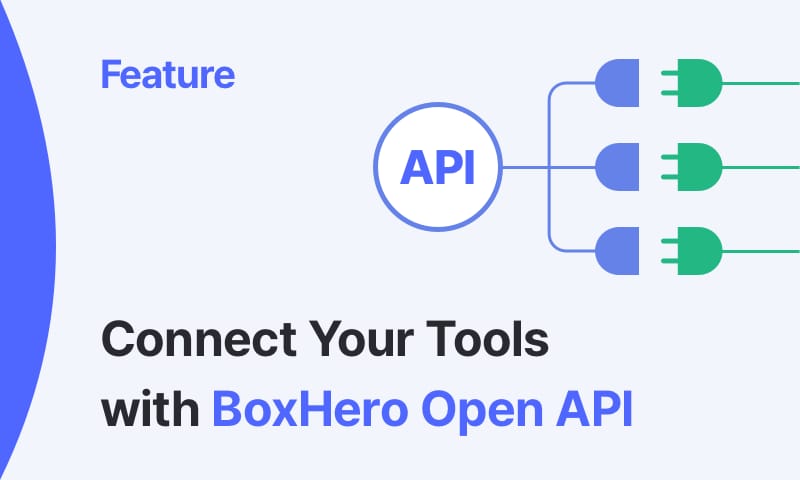
These challenges can be significantly mitigated by adopting user-friendly management systems, establishing clearly defined procedures, and fostering a culture of data accuracy.
Key Takeaways for Your BOM
The Bill of Materials (BOM) serves as an essential tool for accurate product manufacturing, inventory control, and cost management. When managed well, a BOM helps reduce errors, improve communication across teams, and avoid delays.
Modern software tools like BoxHero make this easier by giving you a clear view of what goes into each item, what’s in stock, and what needs to be ordered. With the right setup, you spend less time fixing problems and more time moving work forward.
Understanding how your BOM fits into daily operations and keeping it up to date is one of the simplest ways to keep production on track and make better decisions as your business grows.