Planificación de Requerimientos de Materiales (MRP) Explicada
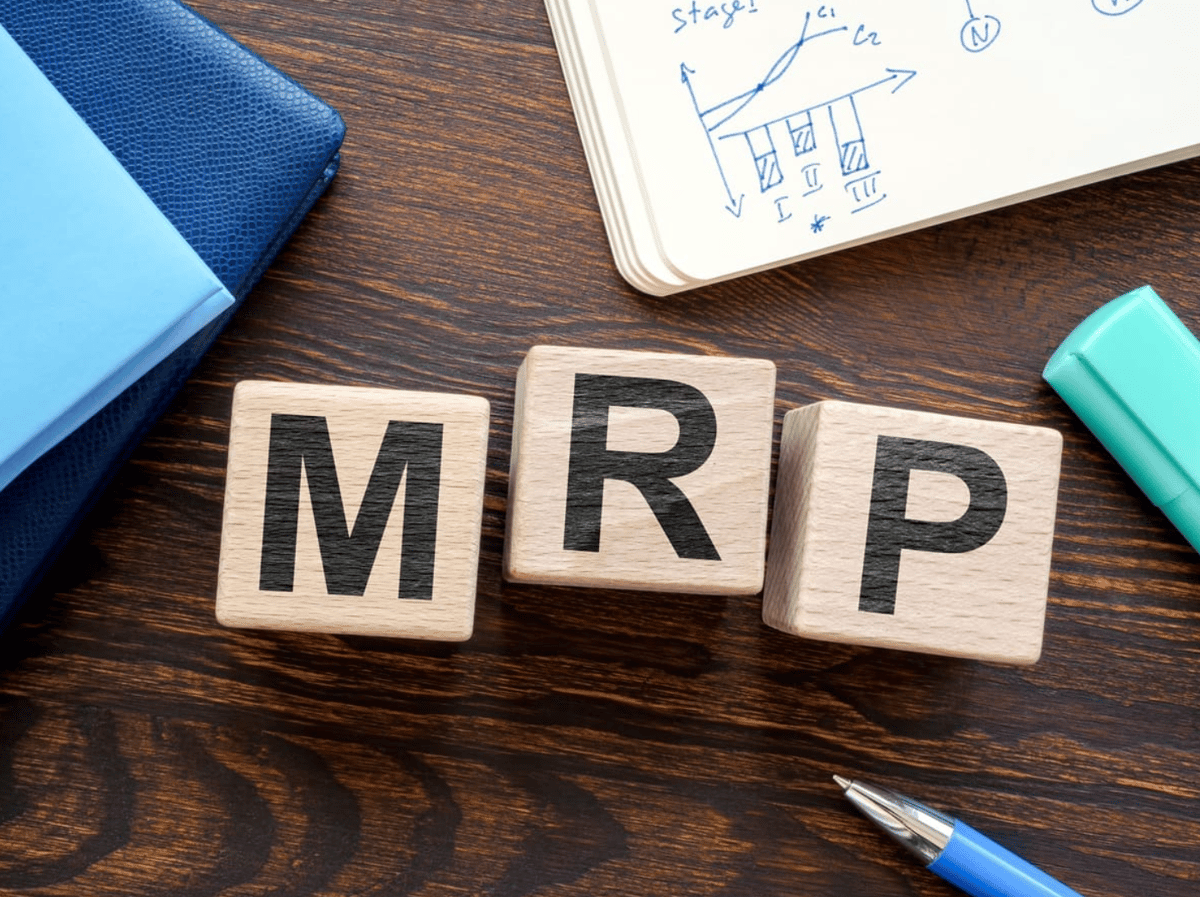
La gestión de materiales: clave para una producción sin interrupciones
La gestión de materiales es uno de los pilares fundamentales para una producción fluida. MRP es un sistema que surgió para gestionar los materiales de manera eficiente, planificando cuánto y cuándo se necesitan los materiales para la producción. ¡Veamos más de cerca el concepto y los beneficios de MRP y cómo puede ayudar a las empresas a aumentar su eficiencia productiva!
Sistemas MRP: materiales correctos en el momento correcto
¿Por qué es tan importante la gestión de materiales en el proceso de producción? Porque no se puede fabricar un producto terminado si falta alguna de sus piezas. Algunos fabricantes mantienen un gran inventario para asegurarse de no quedarse nunca sin materiales, pero esto puede generar fácilmente desperdicio innecesario. Si esta ha sido tu forma de gestionar los materiales, es una buena idea familiarizarse con el concepto de MRP.
Material Requirements Planning (MRP) es un método de planificación para utilizar los materiales de forma eficiente. El término fue acuñado por Orlicky a mediados de los años 60 mientras trabajaba en IBM. En términos sencillos, MRP consiste en calcular qué materiales se necesitan para fabricar un producto terminado. También tiene en cuenta cuántos materiales deben estar disponibles dentro de un período de tiempo determinado.
Para saber qué materiales se necesitan, en qué cantidad y en qué momento, primero es necesario estimar cuántos productos terminados se deberán fabricar. Para aplicar MRP, se necesita crear un Master Production Schedule (MPS), que es un plan de la cantidad de productos terminados que se pueden fabricar en un periodo específico. La demanda se pronostica a partir de datos históricos como pedidos y ventas.
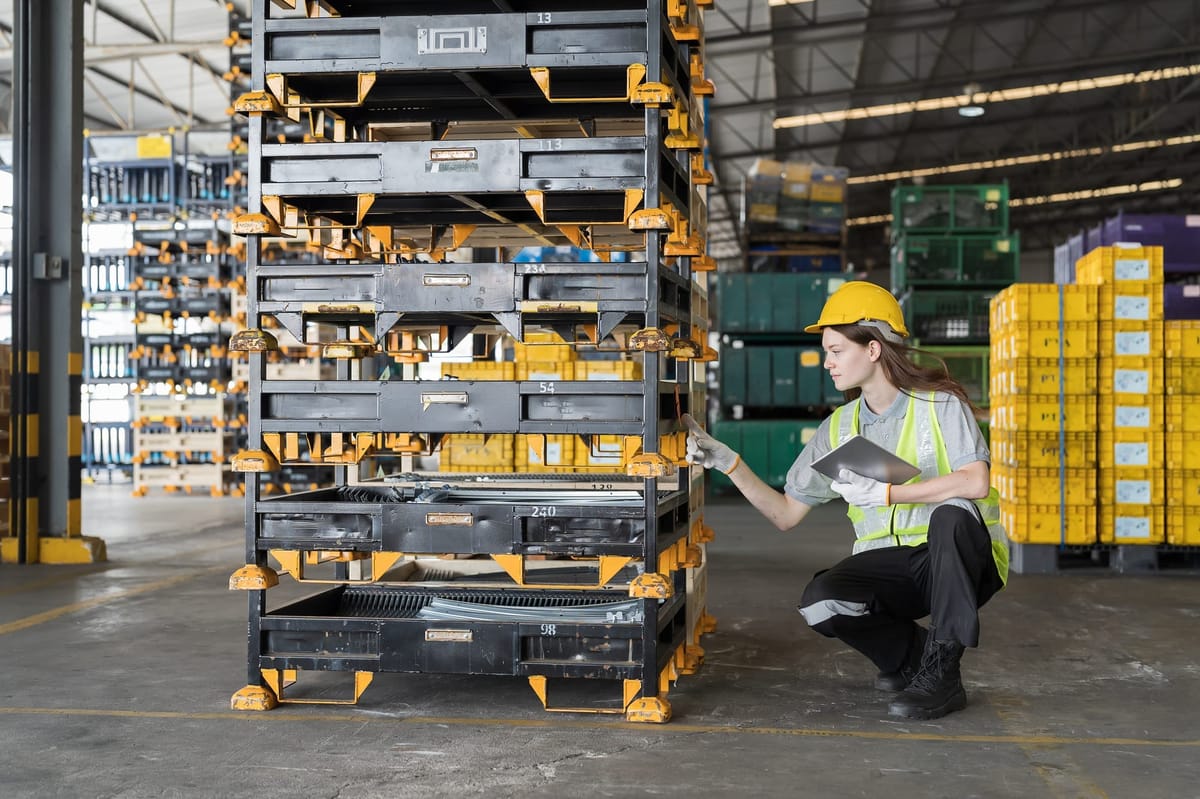
Una vez que tienes un plan de producción para tu producto terminado, es momento de crear un bill of materials (BOM) y planificar las unidades de materiales. Una bill of materials es una lista detallada de todas las piezas que componen un producto terminado. Los fabricantes utilizan el BOM como guía para crear un plan de demanda de cada material, que incluye la cantidad necesaria, la fecha en la que se necesita y el tiempo requerido para obtenerlo.
Este proceso de optimización mediante el MPS y el BOM para conseguir los materiales adecuados en el momento justo es la esencia de MRP. Para optimizar aún más la gestión de materiales, es fundamental supervisar constantemente el proceso de producción real y realizar mejoras continuas.
Ejemplo práctico de aplicación de MRP
Veamos más de cerca cómo se aplica un sistema MRP a través de un ejemplo. Imaginemos a un fabricante de ordenadores, A, que utiliza MRP para mantener fluidez en su proceso de producción. Primero, crea un plan de cuántos ordenadores necesita fabricar cada semana (MPS). Basándose en datos de ventas anteriores, decide producir 10 ordenadores por semana.
Para fabricar un ordenador, el fabricante necesita una unidad de cada uno de los siguientes componentes: placa base, CPU, RAM, disco duro y tarjeta gráfica. Anotan estos componentes en una bill of materials, comparan esa lista con el inventario disponible y revisan las cantidades. Si necesitan 10 placas base, pero solo tienen 3 en stock, realizan un pedido adicional de 7 unidades. Más adelante, si la demanda semanal es superior a la prevista, se ajusta el MRP en consecuencia para adaptarse a las nuevas necesidades.
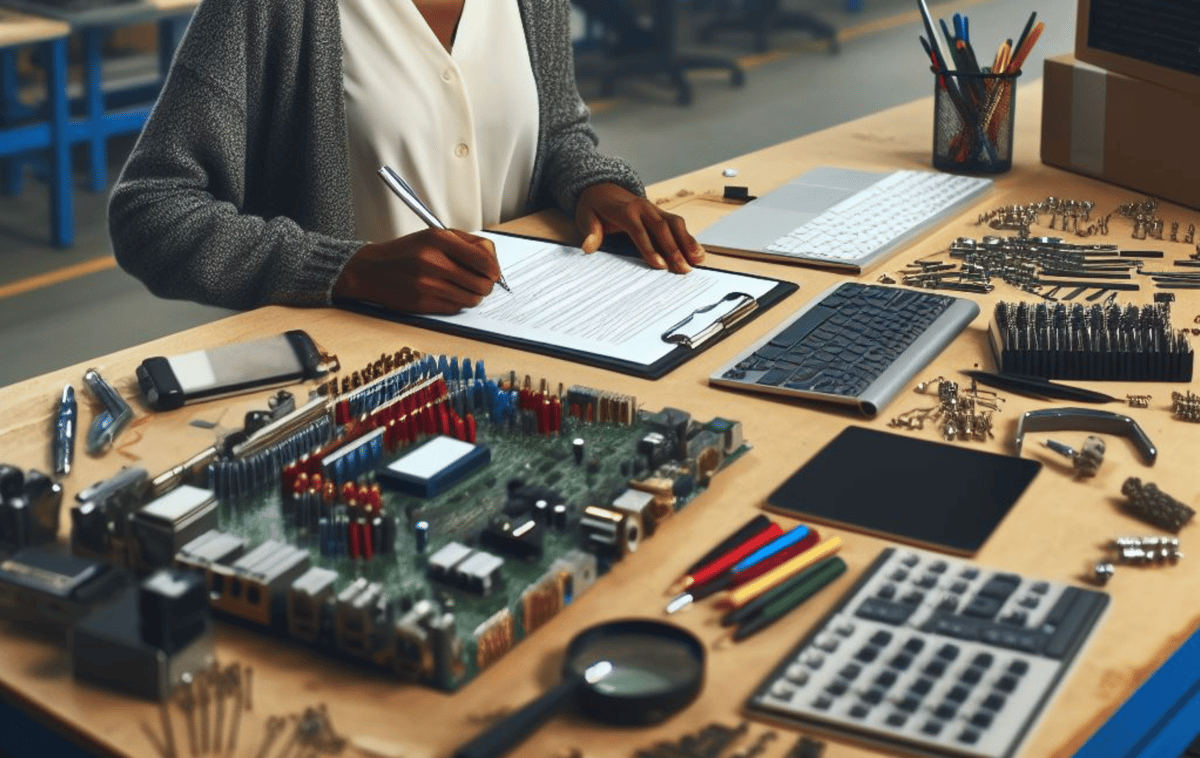
Ayuda a reducir costes, pero tiene limitaciones para afrontar la demanda
MRP tiene muchas ventajas cuando se trata de gestionar eficientemente los materiales necesarios para la producción, incluida la reducción de costes. Permite reducir costes innecesarios al solicitar la cantidad exacta de piezas en el momento preciso según un plan sistemático; disminuye los costes de inventario al optimizar la cantidad de materiales almacenados; y mejora el servicio al cliente al evitar retrasos en la producción cuando se dispone de los materiales necesarios.
Pero el MRP también tiene algunas desventajas. ¿Qué ocurre, por ejemplo, cuando un producto se renueva y las piezas necesarias para su fabricación cambian o se añaden nuevas, y el BOM no se actualiza con estos cambios? Debido a la naturaleza del MRP, que planifica los materiales en función del producto terminado, cualquier inexactitud en el MPS o el BOM puede afectar a todo el proceso de producción. Además, si existe una cultura organizacional con silos departamentales que impiden compartir información de forma instantánea, el MRP puede provocar retrasos en la producción.
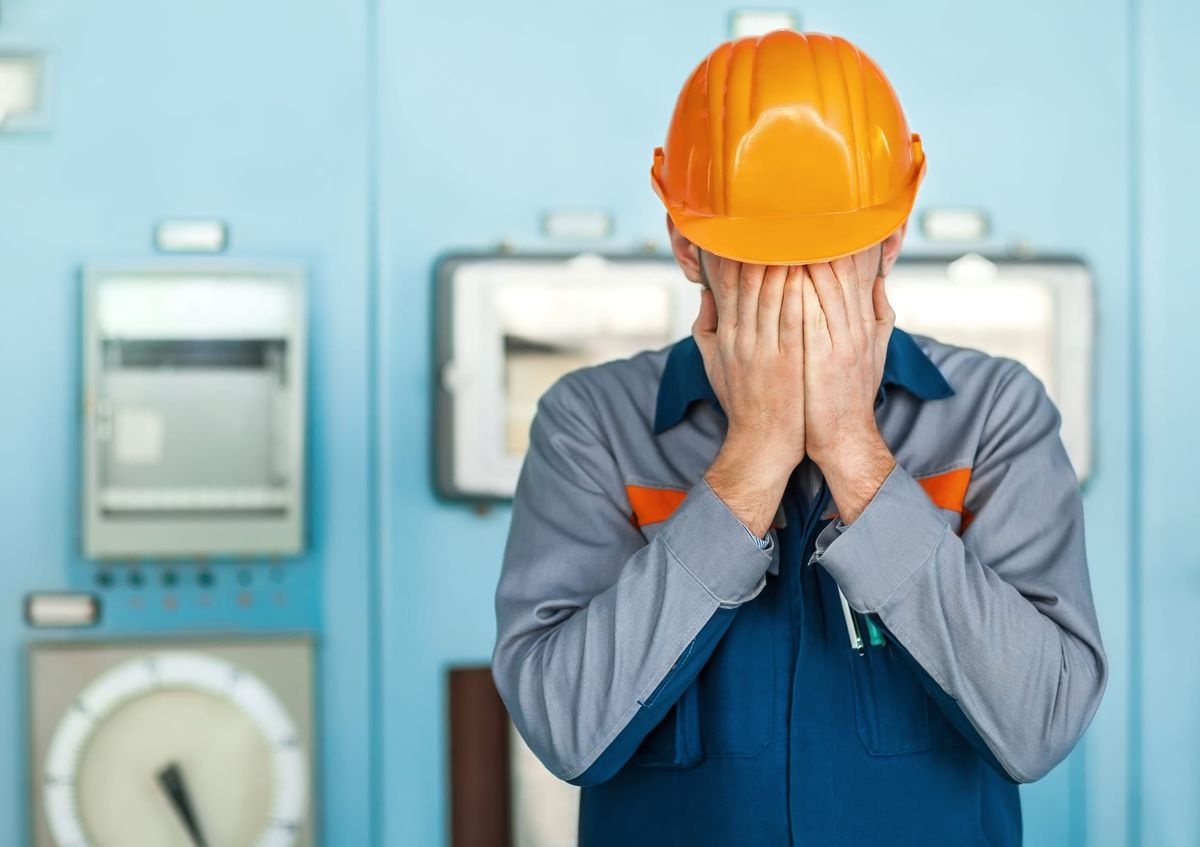
Además, la previsión de la demanda basada en MRP tiene la limitación de que resulta difícil afrontar cambios repentinos en la demanda. Un método como el MRP, que asegura el inventario por adelantado según el plan de producción antes de que se produzca la demanda real, se conoce también como un proceso push. Este proceso push presenta la desventaja de que no es fácil responder de manera flexible ante errores en las previsiones o cambios imprevistos en las condiciones del mercado.
Por ello, hoy en día, las empresas están mejorando la eficiencia de sus procesos productivos mediante el uso del sistema JIT (Just in Time), que es un proceso pull en el que se recibe el inventario tras producirse la demanda real, el sistema MRP II, que integra la planificación de capacidad y de recursos productivos con la planificación del consumo de materiales, y el sistema ERP, que realiza la planificación de recursos a nivel empresarial.